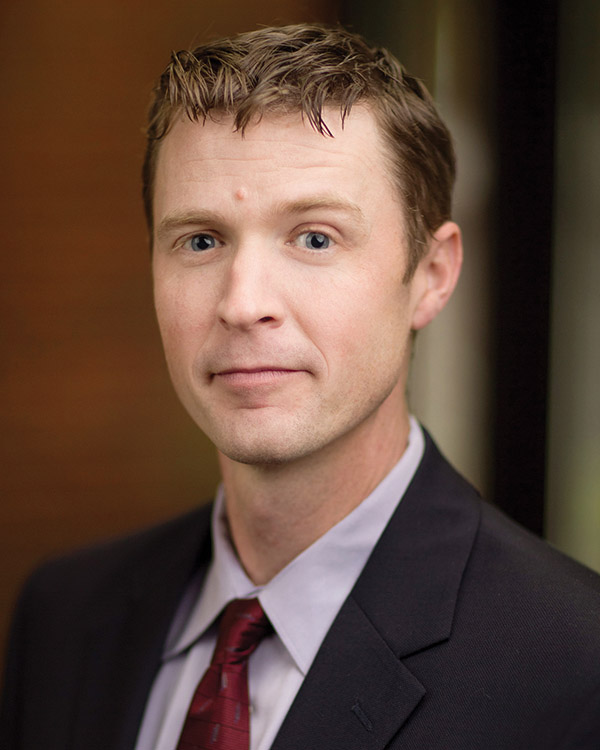
Projects involving renovations to existing commercial and industrial facilities are often challenged to minimize disruptions to active operations. Overcoming this challenge can require accelerating construction schedules and selecting construction practices and planning sequencing to minimize impacts on operations. These projects are further complicated when renovations involve foundation work where foundation support techniques are limited by overhead clearances and vibrations as well as the existing ground conditions. As part of a mezzanine expansion program at two active UPS shipping distribution facilities, the project team was able to address these challenges by utilizing low vibration, driven ductile iron piles in place of traditional drilled micropiles and helical piles.
Ductile iron piles are a low-vibration piling system installed by driving modular 5-meter long sections of specially-designed ductile iron piles. Unlike traditional driven piles, the system is installed with high frequency percussion energy that minimizes vibrations during driving to allow installation within and adjacent to existing facilities. The piles can be installed in a variety of soil conditions. Capacities are developed through either end-bearing on very dense soil or rock or by using frictional capacity developed by driving an oversized grout cap while continuously pumping cement grout to form a reliable grout-to-ground bond zone.
At the Hartford, Connecticut location, the mezzanine design added 13 new column locations. Column design featured compression loads of up to 400 kips along with both tension and lateral load demands. Soil conditions consisted of dense granular fill up to 9 ft. followed by very soft to stiff clay, silt and organic silt extending between 16 and 27 ft. below grade. The cohesive layer was underlain by loose sand and silty sand followed by dense glacial till. Rock was encountered at depths of about 26 ft. up to 40 ft. Groundwater was measured at 4 to 9 ft. below grade.
Project documents specified 7-inch diameter, rock-socketed micropiles with a capacity of 50 tons (compression) and 15 tons (tension) be installed for new foundation support. Geotechnical engineer, GZA GeoEnvironmental, Inc. also included in their report an option for ductile iron piles designed to achieve comparable working capacities. General contractor, CVMNEXT Construction, evaluated different foundation options and selected ductile iron piles to provide cost savings and limited installation duration based on a previous positive experience at another UPS facility in N.J.
The ductile iron pile solution developed by Helical Drilling delivered a 1:1 replacement of the micropiles. The design consisted of a Series 118/7.5 pile (118 mm outer diameter with 7.5 mm wall thickness) installed with an oversized 220 mm (8.5 inch) conical grouting shoe to allow grouting of the pile interior and the annular space along the pile exterior during driving. The piles were designed to support compression loads by terminating after achieving set on rock while also developing frictional capacity to resist tension loads through a grout-to-ground bond zone. A 1-inch diameter Grade 75 threadbar was installed full-length in the center of the grouted piles to resist the tension loads.
Following localized saw-cutting of the existing slabs and excavation of pile cap locations, a total of 79 piles were installed with average lengths of about 27 ft. Piles were installed by cutting the modular 5 meter sections and using compression couplers to work within areas of about 20 ft. of overhead clearance. Full scale load testing showed about 0.2 inches of compression movement at 100 tons and about ¼-inch of tension movement at 25 tons. All load testing and production installation were completed in only 10 working days to limit the impact of the foundation installations on the active operations.
Only an hour down the road at the Stratford, Connecticut location, a similar mezzanine construction plan required support of 18 column locations with loads up to 180 kips combined with both tension and lateral loads. Soil conditions at this location included up to 7 ft. of dense granular fill followed by medium dense sand and gravel to depths of nearly 30 ft. Groundwater was only about 5 ft. below grade.
The plans called for a helical pile system to provide working capacities of 30 tons (compression), 10 tons (tension) and 2.5 tons (lateral). CVMNEXT Construction elected to continue with a ductile iron pile value engineering approach which provided the same capacities, but reduced the potential for unanticipated capacity or installation issues with the helical piles in the saturated sand and gravel.
The ductile iron pile design again delivered a 1:1 replacement of the specified pile loads to avoid any foundation redesign. Because the pile loading demands were lower than at the Hartford project, a Series 98/6.0 pile with a 180 mm (7 inch) conical cap was installed to develop full compression and tension capacity in friction. The pile with its grouted perimeter produces significant and reliable friction capacity from the combination of densification during driving and the grout-to-ground bonding. A 1-inch diameter Grade 75 threadbar was installed full-length in the center of the grouted pile to provide tension resistance.
Tension load testing on a 24-ft long, non-production pile exhibited about 0.3 inches of movement at 30 tons (100% of compression load) and about ¾-inch of movement at 60 tons (200%). Only 9 working days were needed to install nearly 80 production piles along with test pile installation and load testing.
While no foundation technology is the silver bullet on every project, the ductile iron pile system provided the project team with foundation support solutions on these two projects to address the challenging logistics while also delivering economy, rapid installation and reduced risk for unanticipated performance or issues.
For more information on ductile iron piles, please visit www.duroterra.com or www.helicaldrilling.com.
Brendan FitzPatrick, P.E., is director of engineering and marketing for DuroTerra, Braintree, Mass.