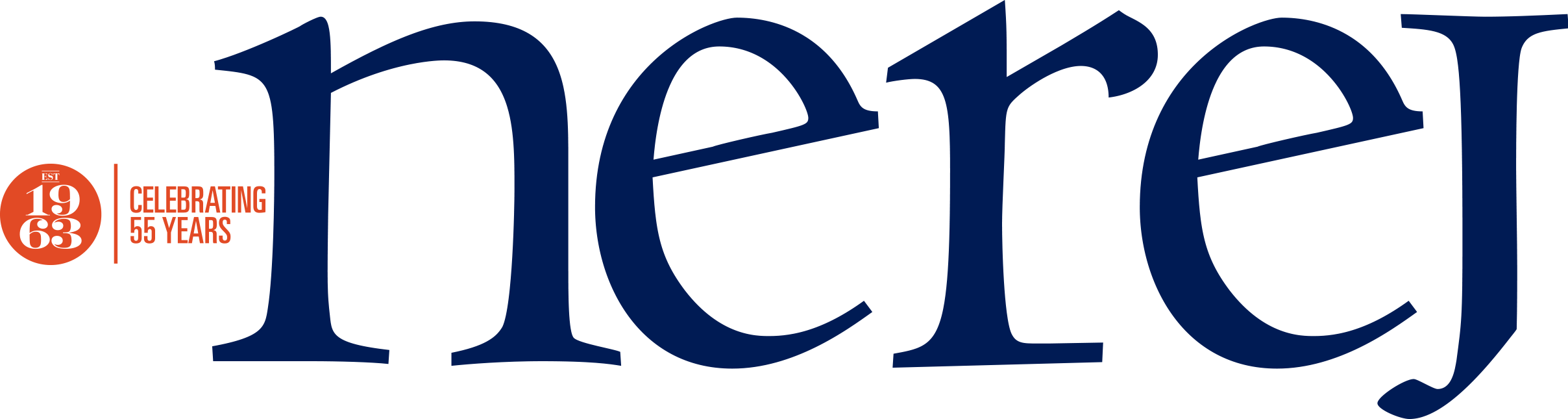
October 29, 2008 -
Spotlights
Value engineering, or value management as it's sometimes called, often has a negative connotation in the architecture, engineering, and construction industries. Many professionals associate it with "cheapening" the original design of a building to cut costs - taking away higher quality materials in order meet a budget. While cost savings is sometimes an aspect of value engineering, it encompasses so much more than just that.
The real goal of value engineering is to research alternative materials and methods that are cost-effective, yet maintain the design intent. In fact, sometimes a Value Engineering alternative may cost more up front, but adds value to a project in the long run - like specifying more efficient HVAC units or more durable windows. The process begins during preconstruction and continues through to project completion. A construction manager will perform an extensive cost analysis at early scope definition and again at later stages of the design with a view toward maximizing function and minimizing cost. This process is most effective when applied to items that:
*Are heavily used during the life of the facility;
*Affect the life cycle cost; and
*Can be incorporated into the design without significant compromise to the project concept, budget, or schedule.
The following three case studies exemplify how value engineering not only delivered the intent of an architect's design at a budget the owner could afford, but also enhanced the value of the project.
Hillside School Academic and Health Center - Marlborough, Mass.: Hillside School is an independent boarding and day middle school for boys in grades 5-9. In 2007, Erland Construction was hired to build the new academic and health center - a single-story structure comprised of a 1,200 s/f health center; nine classrooms; an exercise room; locker rooms; offices; a one and a half-story glass reception room; a multi-purpose/wrestling room; and a student commons.
During preconstruction, Erland performed a thorough value engineering exercise with the school to ensure that the building - as it was designed and specified - would meet the school's budget and program expectations. As with most value engineering undertakings, some aspects of the original design were eliminated to reduce the budget but, more importantly, Erland suggested some alternatives that not only saved the owner money, but also preserved the integrity of the design. One recommendation was to use a thinner gauge of Reinzinc - a material used to clad exterior walls. The thinner version of Reinzinc offers the same exact look and feel as the thicker version, as well as the same level of durability, but it is much less expensive. That one alternative saved the school $40,000 - allowing them to add more program to their new academic and health center. Without the benefit of value engineering, the school would not have known about that alternative material and would have paid the premium for the thicker style.
CenterPoint - Waltham, Mass.: For this rehab of a 187,000 s/f office building Erland provided value engineering during an extensive preconstruction period. From March to late September, Erland worked with owner/developer TC Saracen to research alternative materials and processes to ensure that they would get the best and most efficient building possible for the best value.
The most notable change on this project was the development of an alternative design on an aesthetic part of the architectural concept that ended up saving the client approximately $100,000. The architect had originally designed several large walkout bays, but they were very expensive. After much discussion, the project team determined that the purpose of the walkout bay was to create a certain external visual effect and not for any structural reason.
So, the project team decided to change the walkout bay to a bump out, thereby maintaining the same visual effect, which ultimately reduced structural steel requirements and saved time and money. In the end, everyone was satisfied with the solution - a dynamic focal point is still there, but at a cost the owner can afford.
Massachusetts Maritime Academy Cadet Residence Hall - Bourne, Mass.: This LEED Gold project consisted of adding two floors to two of the existing dormitories on campus while they remained in use, thereby increasing capacity by 150 beds without taking away sites for future development needs. A single-story connector building that united the area on the first floor was demolished and then rebuilt into a 6-story structure to house a new elevator.
As with most school projects, the schedule for this expansion and renovation was tight. Erland worked diligently with the school during preconstruction to ensure that all the specifications, materials, and processes would yield the desired result while not only preserving the budget, but also the drop dead date to turn the building over. One of the major issues was the time constraint associated with soldering the pipes. It's an absolutely mandatory process, but both the school and Erland were hoping to find a reliable way to get it done faster.
Erland's coordination department researched alternative solutions and, ultimately, collaborated with the plumbing subcontractor that was providing all the domestic hot water in the eight mechanical rooms to identify another avenue. Instead of soldering the copper pipes, the team suggested a compression technique called Pro Press that is just as reliable as soldering, but takes 1/3 of the time to complete. This is a unique example of value engineering because Pro Press costs more upfront - the fittings and equipment are significantly more expensive than soldering - but the process is so much more efficient that the school saved a substantial amount of money on labor and the team was able to comfortably meet the schedule.
In all of these examples, value engineering ultimately made the project better - adding significant value for the client. So despite its sometimes unfavorable reputation for merely reducing costs by reducing scope or using lower quality materials, Value Engineering isn't something to dread, but rather a process to embrace.
Rick Jensen is group manager at Erland Construction, Burlington, Mass.