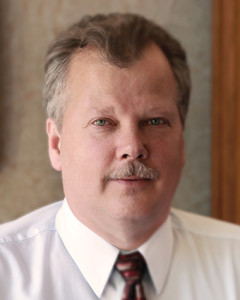
THA Architects, LLC
There are several protocols for addressing the carbon impact of design and development, the most well-known being LEED, and Passivhaus (on this side of the pond, Passive House Institute US). Here are some things to consider – and we’ll highlight a common sense third way.
One should note that LEED, by considering comprehensive environmental considerations, has the effect of improving the impact of carbon indirectly. LEED does not specifically focus on the carbon embedded, ie, sequestered, in the building materials.
Passivhaus – or the less fussy (and less costly) Pretty Good House standard – is increasingly focused on the carbon embedded in the construction materials as part of the carbon cost.
An obvious example would be that you can get LEED certification for a 6,000 s/f single-family home, but that home has significantly higher amounts of carbon embedded in the facility itself as compared to a less ostentatious, and still more than adequate, 2,400 s/f home.
The LEED points are acquired by adding pricey technology to compensate for the extravagant size, but this does not offset the embedded carbon which consumes more than double that of the Pretty Good House/Passivhaus structure. And if that house is built in the middle of the woods, well there goes that much more carbon.
Now, we’re not advocating for a carbon-free existence. We know something about physics, and moreover, we ourselves are carbon-based life forms – but we are arguing that we can (and should) be significantly more carbon-aware. And when treated as a cost, we could consider it something to be managed as carefully as our bank accounts.
Pretty Good – good enough?
The Pretty Good House standard challenges designers to be effective, without regard to virtue-signaling achievements, such as a LEED rating or PHIUS certification.
In a cheeky post on the PGH website they note:
“the 2.0/Low Carbon Edition is meant for thought, discussion, and action, not for check boxes, awards, or membership dues. As always, however, if you feel that you deserve a plaque, feel free to buy yourself one.”
The basics start with minimizing (or eliminating where possible) carbon-intensive materials: concrete, foam, and combustion appliances.
Concrete, of course is difficult to eliminate, but the use of piers and footings in select areas can make significant reductions.
In terms of what you can add, consider common sense use of rigid phenolic foam insulation, off site fabrication, and placement of the house to maximize photovoltaic exposure.
None of the PGH standards come at the cost of comfort, though extravagance is minimized. You can’t sell carbon efficiency to your clients, so PGH adds “If you’re a designer or builder, sell the comfort aspect of a PGH; many clients do not understand or want to hear about technical details or climate change.”
You can read more about Pretty Good House at greenbuildingadvisor.com/article/pretty-good-house-2-0.
Scoring points
The foregoing doesn’t preclude racking up LEED points or gaining Passivhaus certification. The goals of all three systems overlap to a high degree – and all to achieving the same goal: to keep carbon in the ground. They differ in degree, focus, and cost, but are united in that objective.
In fact, you could decide that combining the operational efficiency of Passivhaus with PGH minimal carbon material considerations would be a powerful two-fer.
Add the large-scope considerations of LEED – citing the project near transportation, solar orientation, water management, etc..., and you have a maximal impact in terms of environmental, energy, and carbon efficiency. Plus the points and certifications can add to the resale value of a property. So maybe PGH needs to come up with a plaque?
Payback
There is some discussion about what the carbon payback is. A commonly cited issue is that of wind towers, a source of passive energy generation. But those towers are built of steel, stuffed with foam, and turned by carbon fiber blades.
The carbon impact of this energy source is not zero, and factoring maintenance, it is likely that some installations will not recover their own costs, carbon or otherwise.
Though Passivhaus claims that the energy efficiency of a PH-certified structure will pay for the carbon embedded in the materials within a year, a University of Oregon study advises the payback is seven years in the U.S., both for reasons of climate extremes here that do not obtain in Europe, and to more relaxed building standards. The university also notes that PH buildings will usually have lower embedded carbon than conventional construction.
But when success is achieved in keeping carbon in the ground, maybe “payback” is the wrong term. We could be said to be “paying it forward.”
Thomas House, AIA, is principal of THA Architects, LLC, Stratham, N.H.