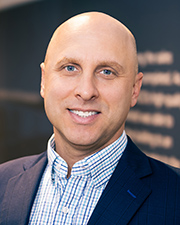
In 2023, demand for distribution and warehouse space stabilized nationwide as a backlog of space from pandemic record highs hit the market and financing became more difficult. However, key regions like New England have continued to see an active industrial market with ongoing demand and low vacancy rates. Leasing for large blocks of space has slowed, but demand for space continues with a trend toward smaller footprint and multi-tenant facilities. The industrial market has also seen resiliency in industries requiring specialty space, such as manufacturing and cold storage. As these trends continue, it will become critical for developers and end-users to partner with an experienced industrial contractor with a focus on complex project types like those in food and beverage, pharmaceuticals, and life science.
1. Key markets nationally are still seeing speculative development with a trend toward smaller footprint facilities.
While the volume of speculative development nationally has reduced significantly, it is still occurring in key markets like New England, especially among major players opting for cash investments rather than relying on traditional debt and equity financing. New speculative developments are trending toward smaller footprints, and larger facilities are being built to accommodate multiple tenants as leasing of large blocks of space has seen the greatest slowdown – a trend likely to continue. New England continues to see an active industrial market with more than five million s/f of speculative space under construction in late 2023. While many developments have smaller footprints, large developers are also continuing to pursue campus projects with long-term development potential.
Additionally, some markets nationally are seeing “storage condo” developments, characterized by total square footage ranging from 50,000 to 100,000 s/f, divided into smaller suites of approximately 3,000 to 5,000 s/f.
2. The need for manufacturing space is on the rise as onshoring and advancing technology drive demand for space.
Driven by a resurgence in onshoring and a focus on supply chain resilience, the manufacturing industry is driving demand for industrial space. The resurgence in onshoring has been particularly evident in life science users as companies are strategically relocating their manufacturing facilities closer to their R&D centers. Despite a rise in vacancy rates due to a large amount of construction taking place in the New England market, demand for life science space remains significant. With the excess of existing options, there will likely be a renewed focus on build-to-suit facilities and retrofits of existing spaces.
Additionally, aging assets, combined with government incentives and advancements in manufacturing technologies needed for production of products such as batteries, electric vehicles, solar panels, and semiconductors are increasing the need for new manufacturing space.
3. Cold storage proves resilient as food and beverage and pharmaceutical users experience growth.
Specialty product types like cold storage are also proving resilient, as food and beverage and pharmaceutical users drive demand for temperature-controlled space. In the food and beverage industry, online grocery sales have continued to grow year-over-year since the onset of the pandemic. This, combined with aging existing assets, has put pressure on the cold supply chain as users look to increase capacity quickly. As a result, new developments from third-party logistics providers as well as developers entering the speculative cold storage space are increasing. Additionally, the market is seeing numerous build-to-suit, expansion, and retrofit projects for major players in the foodservice industry as they expand their operations nationally.
Advancing technologies and changing consumer trends within the pharmaceutical industry are also creating a need for cold storage space. For example, injectable products like Ozempic have different storage requirements than traditional pharmaceuticals. As demand for these types of products rises, the need for new temperature-controlled facilities will follow.
4. Partnering with an experienced design-build contractor is essential for success.
As the industrial market continues to see demand driven by specialty users, partnering with a qualified design-build contractor like ARCO with experience in complex project types like those in food and beverage, pharmaceuticals, and life science will be essential for success. This is crucial in helping clients navigate strategic design decisions and ongoing market challenges. Additionally, unlike traditional delivery methods that treat the phases of design and construction sequentially, the design-build process combines quality of design and construction, management of capital expense, and adherence to schedule all under a single point of responsibility. Preliminary design is completed during the proposal process, and owners benefit now more than ever from the speed at which design-build delivery moves.
ARCO is recognized by Engineering News-Record as the #1 domestic builder of distribution and warehouse facilities and the 3rd largest design-build general contractor in the United States.
Parker Snyder is the director of business development for ARCO National Construction – New England, Framingham, Mass.