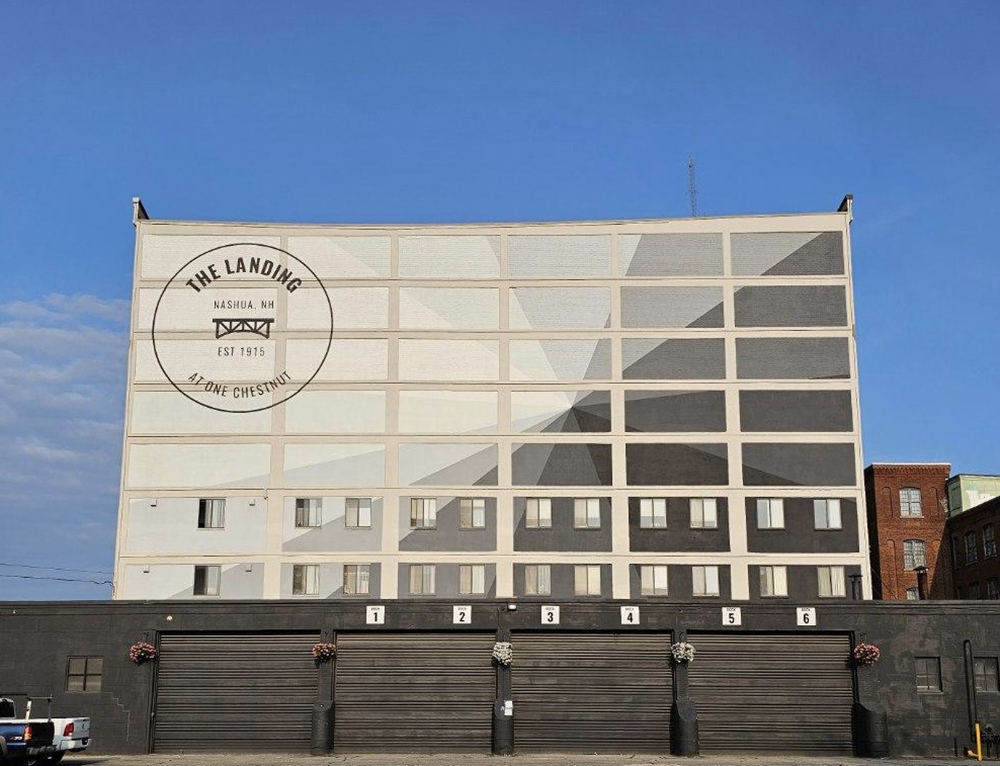
Nashua, NH In 2021 Manzo Freeman Development, owner of The Landing at One Chestnut, engaged Atlantic Restoration and Ganek Architects of Carlisle, Mass. to design and make extensive building envelope improvements of this historic building.
The Landing at One Chestnut was built as a state-of-the-art extension to the Nashua Manufacturing Company to enhance their textile business in the Millyard of Nashua. In 1915 the building was constructed with poured concrete floors and formed concrete walls. The east and west elevations are a combination of concrete columns and spandrel beams with brick sections between them. The building consists of eight floors with 425,000 s/f.
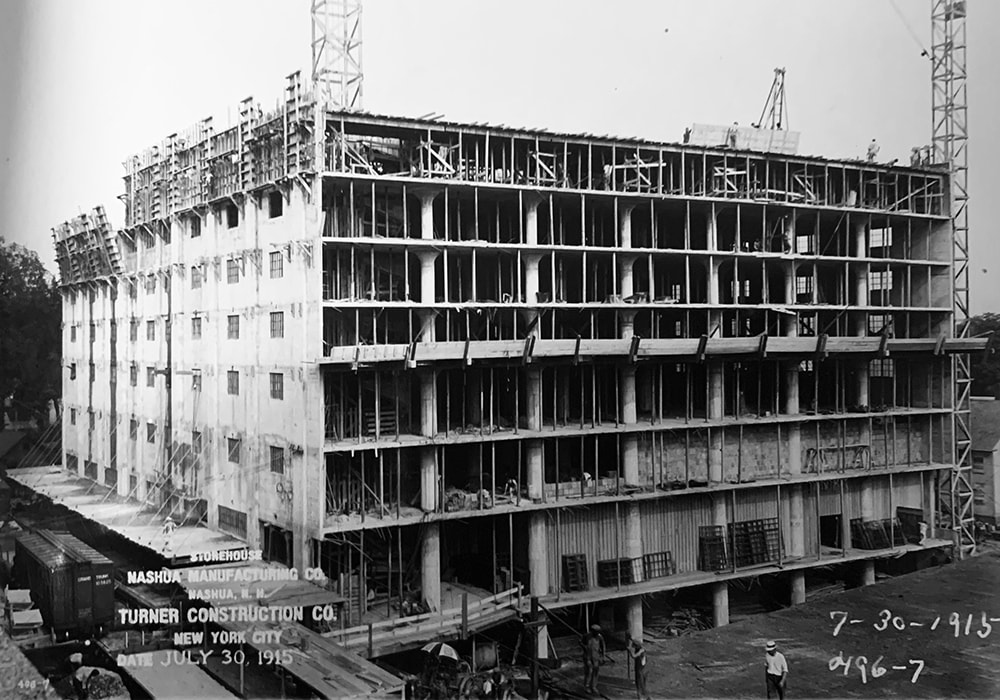
The multi-phase restoration project began in 2021 and consisted of a full façade restoration on the east elevation, partial repairs on the north elevation, and installation of an elastomeric coating along the lower level of the full perimeter of the façade. The scope of work for phase 1 included extensive concrete repairs, joint sealant replacement, masonry repairs including, cutting, and pointing and brick replacement.
ARC installed a unique coating design after repairs were made on the east elevation. The “sunburst” designed by Ganek Architects was installed by priming the entire façade using Beograd’s Multigrip Primer II and using seven custom colors created using Neogard’s Neoflex elastomeric coating system.
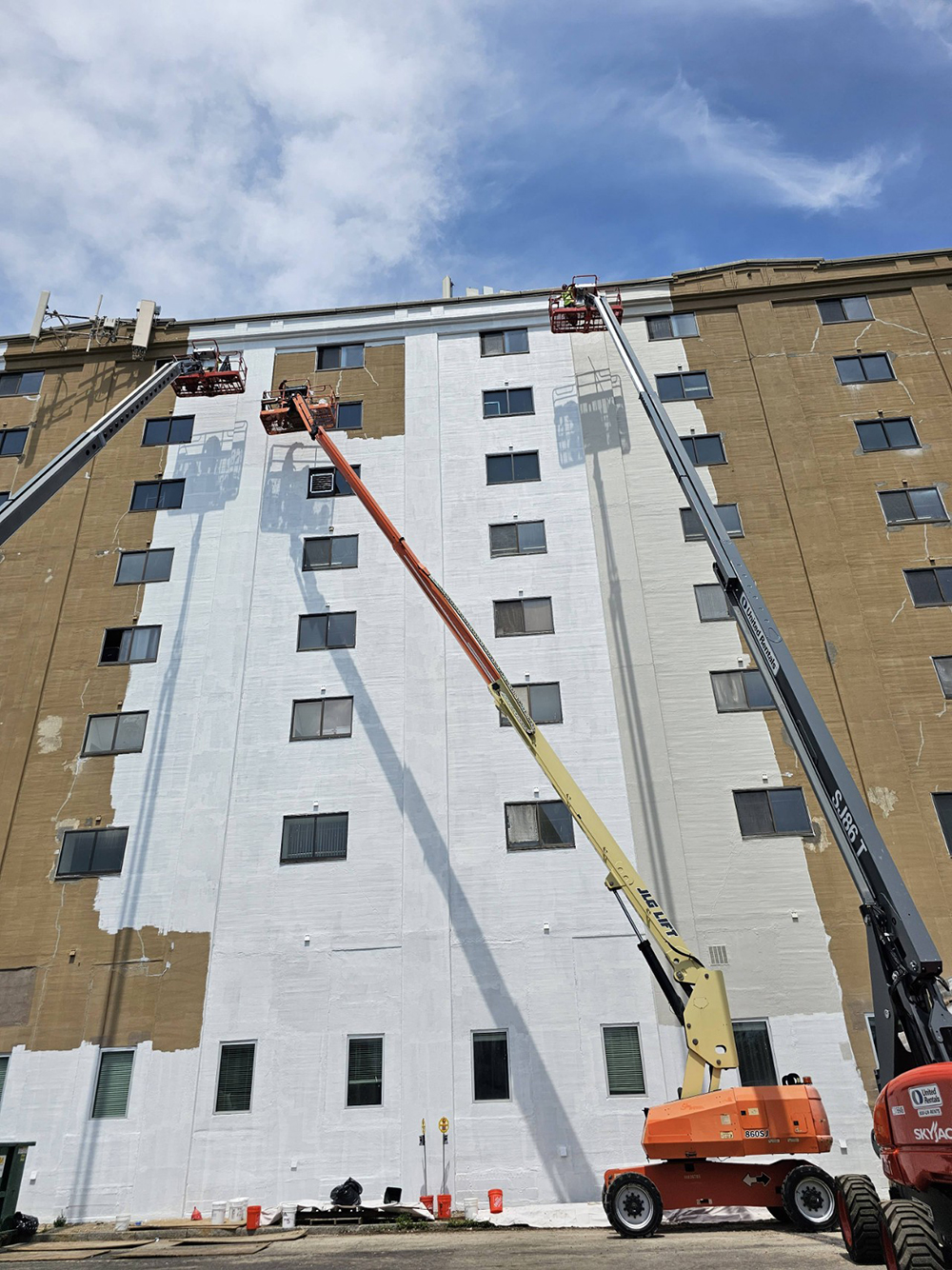
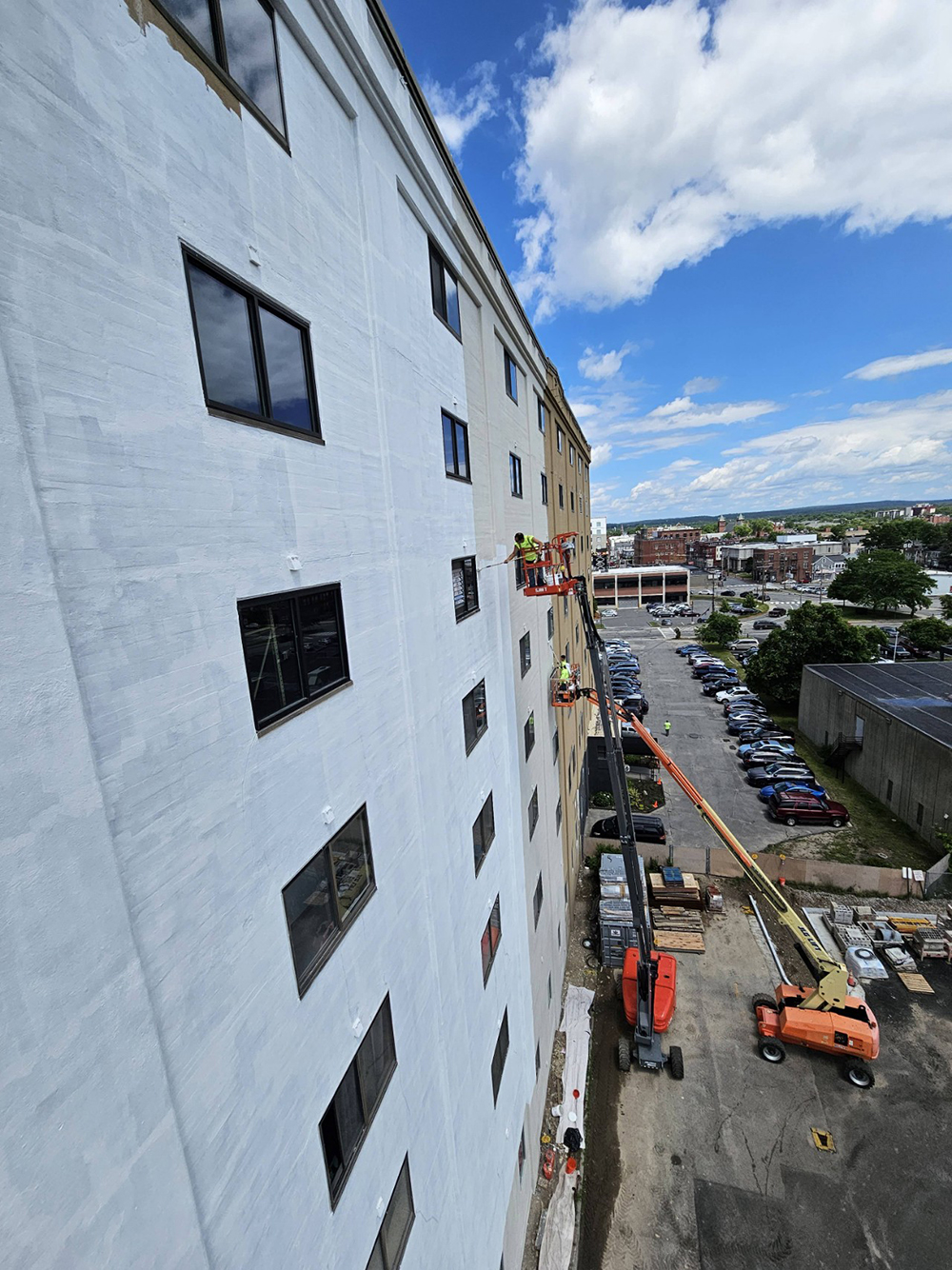
One of the challenges presented during this phase of work was access. Atlantic was able to install roof anchors on the roof of the main building and set up three sets of swing staging on the east elevation in order to map out and install this unique layout. This was a creative strategy that allowed the project to be completed in an efficient manner meanwhile limiting the overall footprint of construction throughout the fully occupied building.
Phase II of this project began in February 2023 and is set to be completed by this summer. This work scope consists of extensive concrete repairs, concrete crack injections, replacement of window sealants and installation of a new elastomeric coating to complement the existing coating that was placed in phase 1 of the project.
All work areas were accessed by use of boom lifts, pipe staging and swing staging. The work was performed while the building was occupied.
Atlantic Restoration, a building envelope contracting firm, restores and re-constructs over 1 million s/f annually.