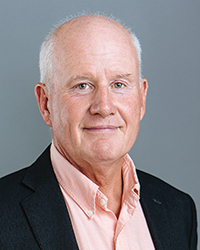
A&M Construction Co.
Working in existing occupied spaces presents additional challenges to construction. Constantly changing regulations mixed with upgrades to existing spaces also adds challenges on top of the specialized constraints of healthcare construction. During the preconstruction phase the construction methodology planned must take all of these issues into consideration.
How to segregate the construction zone from the occupied spaces. Even the appearance of the construction barriers needs to be planned. Ventilation to control both construction area exhaust while protecting indoor air quality of the occupied spaces.
Noise needs to be controlled. Hospitals are in service continuously so noise mitigation needs to be planned similarly to shutdowns. Many systems need to be shutdown such as plumbing to a certain area or testing and this needs specific coordination with the facility staff for the least impact.
Access to the area for personnel, materials and large equipment moved by cranes must be planned while not hampering the use of the occupied facility. Many areas have secure access which again needs special coordination.
Temporary walls used to segregate construction areas. Walls generally need to be at a minimum to provide dust mitigation. Beside normal construction signage aesthetic concerns may need to be planned such as the decoration of the wall adjacent to an occupied space. Access may need to be addressed, sometimes it may be a secure area that needs to be maintained plus permitting access for staff, patients and construction personnel.
Fire protection needs to be maintained.
Material handling has to be well planned. General construction access pathways need preconstruction planning. Large material crane picks need advance planning. Usually large equipment needs to be delivered offsite then brought to the site to be installed immediately. Off hours and weekends are usually needed. Even the location of the crane needs preplanning. As an example, one project needed a revised location planned with a longer reach because the typical location was in front of the emergency room entrance which never closes.
Indoor air quality is regulated by Facilities Guidelines Institute FGI 218 which is part of ASHE 170 on ventilation. The number of air changes in a healthcare facility is higher than in a typical corporate tenant improvement project. The recent regulations Pharmacy 800 also determine final construction project outcomes so a firm well versed in mechanical and clean room construction is preferred. During construction measures need to be deployed to exhaust heavy particle dust as well as many times to also provide HEPA filtered exhaust to ensure a level of cleanness during construction. A firm experienced in healthcare life sciences is also knowledgeable of the methods and constraints of building spaces with negative and positive spaces. The experience of clean manufacturing is essential for building compounding pharmacies to the 800 standards.
In addition to normal construction safety special concerns like personnel protection from blood borne pathogens may need addressing. A firm that has project managers and superintendents trained in this is vital for working in facilities like kidney dialysis centers. Construction personnel need to be aware of the different equipment in these facilities and the proper handling.
Older buildings and office spaces converted to healthcare/life sciences present challenges. Structural changes need typical engineering but construction planning is crucial because other areas of the building may be affected by structural changes and may be occupied spaces needing temporary isolation. Exterior modifications like providing new elevators with ADA compliance and room for stretcher access add design and construction constraints. The difference floor heights and shaft space add another hurdle to preconstruction planning and final execution.
Materials and equipment used is wide ranging and typically extremely specialized. Having an experienced team of subtrades is important for successful project delivery. In addition to planned shutdowns additional shutdowns need to be planned for special testing of equipment. Factory acceptance testing as well as Site acceptance testing may be required and needs coordination.
Healthcare and life sciences construction in existing occupied facilities presents many unique challenges. Working with a firm that can identify and has the experience in these buildings is obvious. To ensure quality timely valued project delivery working with an experienced firm is critical.
Woody Kemp is the director of business development with A&M Construction Co. Inc., Wakefield, Mass.