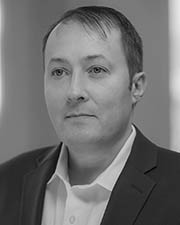
COVID-19 has created a new reality, and the construction industry has been confronted with a unique set of challenges. Safety is without a doubt everyone’s number one priority, and we all need to have a clear understanding of how to protect our people and to safely manage a worksite. As we navigate this new environment together, this focus will continue to guide decisions as they relate to safety, quality, and adherence to cost and schedules.
Construction Site Impact
In a post-COVID-19 world, the pre-construction phase of any project will be more vital to a project’s overall success than ever before. Our recommendation is to take the time to address issues like logistics, trade planning, scheduling, waste flows, and employee flow. All are essential and will help to maintain social distancing, adhere to cleaning requirements, and meet the overall goals of the project.
Modularization is a great way to allow contractors to work remotely in their shops and facilities to advance the project while limiting their exposure to potential seen and unseen hazards at the job site. By shifting work to vendors’ facilities, the risk of COVID-19 exposure (through social distancing, area segregation, HVAC filtration, shift work, etc.) can be more easily and cost-effectively addressed than on the job site.
Onsite Safety
The pandemic has facilitated the discovery of creative ways to manage tasks that are typically multi-person or team tasks. Innovative uses of equipment, tools, and materials have helped to reduce the number of people needed to complete the task. Other practical ideas that can be easy to implement include:
• Staggered lunch breaks, placing occupancy limits on elevators, and designating staircases unidirectional.
• The continuation of increased sanitary practices – frequent handwashing, the sanitizing of tools and work surfaces during and between shifts, the use of PPE, and ensuring that supplies and tools are not shared.
• The implementation of area designations to help limit the number of people each craft encounters. On larger, more complex projects, area designations are being used to help segregate the workforce and limit each crew to one area per day (unless otherwise approved).
• Social distance monitoring through security badge tracking. If a case of COVID-19 is confirmed, it will be easy to identify everyone the individual came into contact with (within the safe six-foot distance) and communicate this information quickly.
Costs and Schedule
The potential impact of cost and schedule changes need to be considered in the early stages of the project. Items to address such as additional PPE, increased job site cleaning and sanitization, temperature checks, social distancing approaches, logistics considerations, reporting, and the overall encouragement of increased hygiene practices could affect the overall cost and schedule of the project if not handled correctly. We recommend that you consider these factors and build in schedule risk and cost risk factors into each project.
The COVID-19 pandemic has accelerated the adoption of technologies and approaches and could prompt a positive change in the use of these methods by the construction industry.
Carl Bradbury is senior director of construction management at DPS Group, Framingham, Mass.