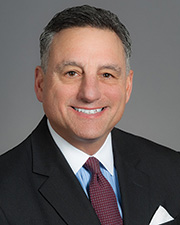
Auburndale Realty Co.
We are several months into the COVID-19 pandemic and many of the same questions are being posed in the commercial real estate industry: How do landlords safely reopen office buildings? Will increased e-commerce use continue to drive warehouse demand? How will tenants and landlords negotiate rent? But another question we should consider has also been the topic of debate for decades: should we bring U.S. manufacturing back home? Due to the current crisis, this question, along with other changes that many never thought possible, could be on the horizon.
A Pending Shift in Shipping
First, let’s look at how current shipping and imports into the U.S. are changing. On a recent earnings call, Maersk shipping predicted that Q2 2020 will experience a 25% decline in Twenty-foot Equivalent Units (TEUs) and a 5% drop in exports. Globally, TEU volume is down 8-10% to date and Asian exports are down 20%. New tariffs on Chinese goods were already causing a decrease, but the global lockdowns made the problem exponentially worse. Combine this with several Chinese factories shuttered due to rising infections and receiving goods from China becomes a challenge. While stay-at-home orders have decreased demand for some products, many others are incredibly hard to find, especially for some critical items like prescription drugs and personal protective equipment (PPE).
The Cost of Doing Business
As the coronavirus looms large, many companies have realized that having all or most of their products produced and shipped from one country or region carries significant consequences. But while the nation groans at long wait times for online products or stares at empty shelves, North American manufacturing is poised for a rebirth, ready to become a potential savior in this supply chain challenge.
In the last five years, U.S. suppliers have been balking at China’s habit of stealing and reproducing patented and licensed items. And while they illegally reproduce goods to sell on their own, the delivery of ordered items to U.S. clients are often delayed, causing contract penalties to U.S. suppliers. The cost of not being able to deliver promised goods to the consumer has become a major pain point for many companies. Even before the pandemic caused so much disruption, U.S. companies were thinking of ways they could bring manufacturing back to the U.S. (commonly known as reshoring). Now, COVID-19 has substantially accelerated this idea. A new survey of North American manufacturers found that 64% want to bring all or some of their operations back to the continent. And this isn’t just a North American trend. A recent SIOR blog about the U.K. industrial sector discussed the desire to bring manufacturing onshore.
Made in the USA? Not so Easy.
Complicating the desire to make products domestically is a shortage of available physical manufacturing space, as many facilities have been redeveloped or retrofitted into a higher and better use in the past 30-40 years as U.S. manufacturing declined precipitously. For all the dormant factories put on hold because of the pandemic, there will be a backlog of demand for existing products once manufacturing resumes, at least in the short term. America’s manufacturing industry has been a hot button issue for years and a major political chess piece for candidates trying to woo voters in regions hit hardest by its demise. But restarting the engine will not be like flipping a switch. For instance, many pharmaceutical companies may want to stop making drugs overseas, after seeing how supply chain issues from China have created a massive shortage in North America. But how long will that transition take? Some experts predict the process of finding, outfitting, and manning and developing enough domestic factories to produce just 50% of current U.S. demand could be as much as two years. A long time to wait for a product that could save someone’s life. However, 3D printing has become popular over the last five years and may be able to pick up the slack.
U.S. Manufacturing’s Long Journey Home
Where there are demand and interest, there’s opportunity and investment to be found. There is a renewed focus and a surge of investment attraction into building new facilities or revamping existing ones. Investor demand for industrial (especially warehousing) and manufacturing property has been steady and should only get stronger. As a sector, industrial CRE is in far better shape than other areas. As of May 8th, the YTD NAREIT U.S. industrial real estate index showed a value decrease of just 2.6%, versus the 43.9% decrease in retail.
To offset the lack of manufacturing spaces in urban areas, Congress introduced Opportunity Zones, offering significant tax benefits for industrial developers. Unfortunately, the plan expires in 2027 and legislators will need to extend the plan to encourage manufacturing growth here at home as a long-term strategy. Otherwise, one of the biggest motivating factors for companies to restart their production in urban areas could go away.
In the Boston market, I have seen manufacturing rents in the last 35 years go from $3 per s/f NNN to $15 per s/f NNN, highlighting both a lack of inventory, higher demand and repurposing land use. For savvy CRE professionals and developers, there will likely be significant opportunities to get on the ground floor of a major market shift and in the process, make “Made in the USA” a common sight on the products we use every day. As for storing and distributing those products, finding appropriate warehouse space is equally challenging. If your company only needs 16-18’ clear for manufacturing and storage, where are you going to find buildings that meet that need? Most facilities have 18-30’ clear with higher rents and occupancy costs. Back in the ‘80s manufacturing sites typically only needed 14-16’ clear ceilings. Buildings today are made for high bay storage at heights that are not needed by low-bay manufacturing. As with manufacturing facilities, the creation of warehouse space presents outstanding opportunities for growth, especially in areas that could use a surge of economic energy.
Will we make the move to be less dependent on supplies of critical items from China? Or is manufacturing at home too costly to make the shift? This pandemic has many people, in many countries, asking the same question. Hopefully, we’ll soon have an answer.
Rob Nahigian, FRICS, SIOR, CRE, MCR, serves as the New England SIOR Chapter president and national ed chair and is principal of Auburndale Realty Co., Newton, Mass.