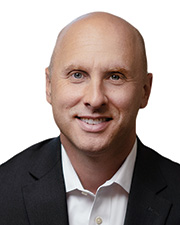
ARCO
Demand for cGMP facilities is on the rise as companies look to gain greater control over their supply chains and keep manufacturing, packaging, and distribution processes close to laboratories and R&D facilities, especially in mature life science markets like Boston and New York. Because of the complex needs of cGMP tenants, there are several key design and construction elements that should be addressed in a project’s earliest stages to ensure a successful development.
Wall Type Selection: While there are many structure types that can be utilized, most commonly, a steel structure is selected as it offers the ability to easily achieve a high-end appearance that end-users often seek. However, tilt-up concrete is also a viable option and is often a much more cost-effective solution. Design elements can be incorporated to elevate its appearance while still maintaining the cost benefits. Both steel and tilt-up can be utilized with various facades such as composite metal panel, insulated metal panel, or curtain walls.
Structural Upgrades: Increased roof loads, mechanical penthouses, and specific bay spacing can be incorporated into a speculative build to accommodate the needs of cGMP tenants. Additionally, the roof can be installed with a vapor barrier to create an environment conducive for lab and cGMP uses. Accommodations for hanging equipment from the building structure should also be considered. While mezzanines don’t have to be included in the initial build, setting up the structure with increased footing sizes to efficiently add them on retrofit is advised.
Advanced MEP Design: cGMP facilities require advanced MEP design to support tenant operations. Greater electrical service is needed to support advanced HVAC systems for temperature and humidity control, as well as tenant manufacturing equipment and processes. Therefore, the infrastructure should be in place for multiple future electrical services. Additionally, flexibility for increased water, sanitary, and gas services should be incorporated into the plumbing design.
Overall Flexibility: Designs should allow for equipment and manufacturing components, as well as necessary utilities, to be easily implemented and updated without the need to adjust the fixed infrastructure. Strategic design decisions such as leaving out areas of the floor for future plumbing and strategically locating knockout panels in exterior walls to accommodate future openings can maximize flexibility and decrease time on retrofit. Tenant amenities such as lobbies and offices should also be considered so that they can be achieved during retrofit.
New England Project Highlight: ARCO National Construction is partnering with Lincoln Property Company on a 120,600 s/f speculative advanced industrial facility in Marlborough, Mass., designed to support the manufacturing needs of potential cGMP and R&D tenants. The facility features bay spacing for installation of cleanroom PODs, increased footing sizes for future mezzanines, electrical service upgrade accommodations, a roof vapor barrier, and more.
Moving Forward with the Right Contractor: A design-build approach like ARCO’s allows developers to make well-informed decisions about cGMP upgrades in a project’s earliest stages. Because the construction team works directly with the architect, costs can be estimated, and the completed project can be accurately conceptualized before significant dollars are spent. Experienced contractors, like ARCO, can offer solutions and alternatives that save valuable development dollars while still making a space suitable for future cGMP tenants.
Parker Snyder is the director of business development at ARCO National Construction New England, Framingham, Mass.