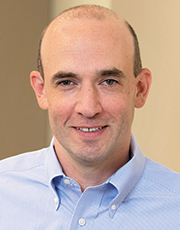
Acentech
So, you’ve found yourself managing a construction project at your institution and somehow it needs to get done while you keep everything running as normal. Don’t panic! While noise and vibration certainly aren’t the only issues created by construction, they are an inevitable change in the environment that people and operations will experience, possibly for several months or even a few years. What can you do to preserve suitable conditions AND accomplish your project? Here are five steps to help resolve the challenge and develop a highly successful approach, even in some of the most incompatible situations.
1) Identify the noise and vibration sensitivities. This may sound obvious, but people closest to the project are typically the only ones who know whether or not there are noise and vibration issues related to the work at hand. Many buildings are built with certain purposes in mind, so these spaces often work just fine for folks on an everyday basis. It’s only when something changes in the environment (like nearby construction) that these end users can experience impacts on certain activities or see equipment malfunction.
Once you’ve identified who has particular needs for noise and vibration, the next challenge is figuring out what those requirements should be. Are those satisfied within the current building already? Are the requirements based on specifications or industry standards on acceptable conditions? Beyond those with functional noise or vibration needs, general nuisance and annoyance rounds out the list. (For the purposes of this article, we are ignoring concerns associated with much higher levels, which would raise flags for hearing damage and building cracks, since these are typically subjected to regulations and addressed for safety.)
2) Determine your limits. Equipment manufacturers, research processes, and industry design guidance are a good place to find requirements, but often the existing conditions are your best bet in setting acceptable limits. However, it’s not the only thing you should rely on since most activities don’t toe the line of what works and what doesn’t. Instead, the everyday background of the site in question helps you to understand the variability in conditions and best ways to characterize what limits and metrics to define as acceptable and unacceptable.
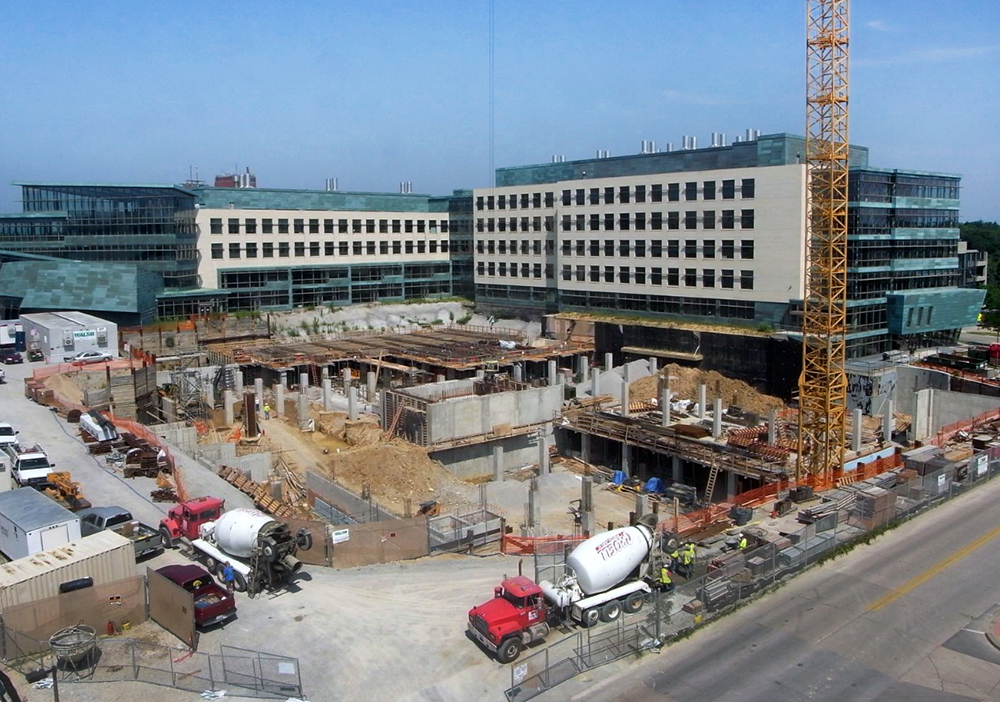
(Photo courtesy of Acentech)
3) Evaluate impact and its impact. With an understanding of actual requirements and planned construction work, try to determine what levels of noise and vibration are likely to occur. Sometimes this can be done with calculation tools and rule-of-thumb engineering, but often the best way to test out the situation is to actually do it. Work with your contractor to identify the tools and methods they’re planning to use, then schedule a time to try them out with staff, starting with the least concerning and furthest away, and then moving closer. What you’ll learn can be both objective and subjective, and will also help to justify decisions, cost and schedule.
4) Consider reasonable measures for mitigation. Before boarding up the windows and moving things across town, many approaches to reduce noise and vibration can actually turn an incompatible scenario into a positive one. Options can include changes such as beefing up windows with additional panes and airspace, or putting lab benches onto air springs that attenuate undue vibrations or actively cancel them out. But don’t be too quick to fulfill requests - make sure to evaluate whether the approach will actually get you to where you need to be, or is even actually needed at all. And last but not least…
5) Sit back and WATCH! After developing limits, mitigation measures, and tweaks to construction planning, you’ll only sleep well at night if you put systems in place to keep it all in line. Remote monitoring programs allow you to continually evaluate and correct as work moves around, and construction tasks and personnel change. The ability to automatically and immediately provide feedback to contractors helps them to work efficiently and optimize resources, while at the same time allows your building operations and occupants to trust they’ll have the environmental conditions they need. If you can do that, you’ve taken a big step in making your project a compatible and successful one for all parties.
Marc Newmark is a principal consultant at Acentech, Cambridge, Mass.