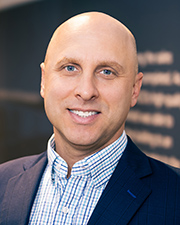
Human behavior and the way we consume goods have changed dramatically throughout the COVID-19 pandemic. Consumers stay home and utilize e-commerce more than ever, forcing companies to focus on strengthening their domestic supply chains, especially last-mile facilities for same-day delivery capabilities.
Even before the pandemic, the control of supply chains was shifting domestically due to rising offshore labor costs, increased automation, and sophisticated just-in-time logistics. The combination of these forces has had a profound impact on the explosive growth of industrial development. Developers, brokers, and investors can capitalize on this market expansion by increasing their knowledge and partnering with an experienced construction team.
Boston, in particular, has felt the effects of this phenomenon with a vacancy level below 3% and only 7-8 million s/f available. The severe supply/demand imbalance has been a result of unprecedented demand coupled with a supply crisis. The lack of developable land in the Boston metro area has made it challenging to create enough new supply to fulfill the needs of regionally growing product types like light manufacturing, biomanufacturing, warehousing, and robotics. New developments require extensive knowledge, creativity, and collaboration to accommodate market demand best, and it is imperative to consider the unique needs of specific building types beyond the standard shell.
Warehouses: High bay warehouses prioritize storage, so rack layouts must account for power and lighting requirements. Speed bays are usually 60 feet and adjacent to the truck dock to stage an entire trailer’s contents in a 60-foot length. With e-commerce distribution facilities, location is critical to achieving same-day delivery capabilities.
Light Industrial: Conversely, a light industrial building may have a minor storage component and serve as space for light manufacturing, production, fabrication, research and development, and office. Because these facilities have fewer incoming and outgoing shipments, they have fewer docks and storage racks but more open areas and office space. Flexibility is key in the successful development, design, and construction of light industrial buildings.
GMP Manufacturing: In the past, developers have considered flex light industrial space for this product type, but they are now pursuing developments specifically to accommodate advanced manufacturing innovations. GMP manufacturing includes products from pharmaceuticals to medical devices to biologics, so more careful planning and consideration are required to meet FDA regulations and receive proper permits. These facilities can have extensive cleanroom requirements and contain enclosed spaces designed with performance requirements for temperature, humidity, and filtration dependent on biological classification. Power is typically upsized, and an outside generator may be required. GMP manufacturing tenants tend to prefer a faster speed to market and need the facility to support both current and future operations in terms of structure, electrical load, etc. GMP developments come with significant capital expenses up front but have the capacity for high rents over long leases.
No matter the type of facility you are looking to develop, working with the right team ensures development success and utilizing a design-build general contractor like ARCO streamlines communication and establishes more effective communication. Through our unique process, facility design is reviewed and assessed by all team members in the earliest stages of a project, allowing for decisions to be made with full knowledge of their impact on cost, schedule, and scope. ARCO’s extensive preconstruction services include risk mitigation, design team coordination, comprehensive cost estimate, site feasibility studies, constructability review, value analysis, future expansion planning, and many more. Our project approach removes the risk of overspending on design and construction by providing clients with a firm price proposal. It yields an average overall delivery speed of 33% faster than that of traditional plan-and-spec construction.
There are many details to consider for successful industrial developments, from high bay warehouses to light industrial space to GMP manufacturing. Infrastructure, power, and HVAC systems are just a few variables that change depending on building usage, so it is essential to partner with a general contractor that understands the nuances of each product type. There has never been a better time to invest in industrial construction in a market with such high demand and limited supply.
Parker Snyder is the director of business development for ARCO National Construction New England, Framingham, Mass.