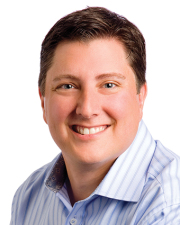
As an industry, we continue to adapt to the changing consumer landscape and seek out new design and construction trends. Hotel developers today experience escalated land and construction costs, diminishing quality, and lengthy time lines. As a result, modular construction has emerged as an innovative building approach due to many benefits including speed, quality, cost, and overall practicality. We see the success of modular construction in a variety of markets like commercial and multifamily housing, institutions, education, healthcare, and retail. This is a long-term industry change that requires all of us to educate and learn from one another.
What does the process entail?
Modular construction involves taking materials and components of a building and partially pre-assembling them in an off-site location, where they are later quickly and easily put together on-site into a fully functioning building. This can include the entire building or components of a larger structure. Modular contractors typically work together with general contractors to leverage resources and take advantage of different types of construction approaches.
This building technique is best suited for new build hotel construction. However, we’re seeing it increasingly used for extensions and annexes. Because of the factory environment of the initial build, it ensures all elements of the module are constructed to meet hotel brand standards using approved materials, fixtures, and furnishings. Having collaborative relationships with modular contractors and bringing them into the process early is key to the project’s success.
What are the different uses for hotels?
There are various methods of applying modular construction to hotel development. With full modular design, entire guest rooms are assembled off-site and installed on-site. Every room element is pre-fabricated and replicated including the walls, windows, carpet, fixtures, accessories, and even artwork. This is particularly useful for hotels seeking to emulate their portfolio properties while adhering to brand standards. Using partial modular, portions of a guest room are assembled as a pod. The pod is then placed into the building, ultimately connecting seamlessly with all electrical, plumbing, and mechanical connections. With system kits, electrical, plumbing, and mechanical systems are manufactured off-site and kitted. For example, a guest room electrical panel system is made with the required electrical panel and wiring. Each kit is labeled for a specific guest room to meet requirements.
What are some of the benefits, risks, and key learnings?
Of course, there are both benefits and risks to using the modular building approach, with more challenges to overcome especially in the early stages of adoption. Some of the benefits include a faster construction process, more streamlined and efficient uses of skilled labor, and less material waste. It’s more environmental friendly – less site damage, material exposure, and landfill waste than with traditional building methods. And, it’s climate neutral. Modular construction typically occurs indoors, away from harsh weather conditions, preventing damage to building materials while allowing builders to work in safer conditions.
One of the risks is that early commitment is required. Depending on when modular contractors are brought into the process, there may be potential barriers with schedule and process changes Start early and engage often with all project stakeholders. To ensure success, this approach begins at the design phase. Second, it requires non-traditional funding. With a modular approach, the bank releases funds before implementation on site. Third, it creates larger buildings. To accommodate the joining of modular units, additional space is needed for infrastructure – increasing the overall hotel footprint. Lastly, because this is one of the newer building approaches, there is going to be some level of apprehension. Avoid dismissing the process because it’s a departure from the norm and take advantage of all benefits of modular.
Currently Group One is involved with two modular projects where the benefits of the speed and accuracy of modular are a great benefit to the overall projects. We find ourselves working closely with the modular manufacturer to ensure we obtain all the benefits of what modular has to offer. Both projects are 4 star resort properties and the speed of delivery was a key factor in making the decision. The high quality and ability to get the project complete in a short off season window.
Modular, here to stay?
Given the many benefits of moving to modular – building smarter, greener, and faster – it’s not surprising that this approach is gaining momentum. It’s a sustainable turnkey solution that dramatically reduces construction time and delivers improved quality and consistency. With developers facing increased land costs and barriers to market, this approach minimizes development costs through shared areas. It’s hard to tell how large of an impact it will have on the hospitality design industry long-term, yet it’s safe to say, the move to modular is here to stay.
Harry Wheeler AIA, NCARB, LEED is a principal at Group One Partners, Inc., an award-winning hospitality design firm based in Boston that specializes in architectural, interior design, and purchasing services for hospitality properties.
Wheeler is a registered architect in more than 15 states and a member of numerous architectural, lodging, and marketing associations.