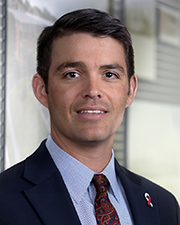
One of the earliest questions that owners, architects, and builders must address when considering a large industrial warehouse construction project in the Northeast U.S. is the building’s envelope. Should your warehouse depend on insulated metal panels (IMPs) or tilt-up concrete? Each project is unique, and answering this question requires a holistic view of all factors at play, including the building’s size, budget, purpose, design, location, and your organization’s specific needs.
Size and Budget: Because tilt-up concrete involves placing steel-reinforced concrete walls on the ground and hoisting these walls up with a crane, tilt-up is only viable when there is ample land available. Because they can be handled with smaller equipment, IMPs are the obvious choice for construction sites where open space is at a premium. Size also comes into play when considering budget.
The primary advantage of tilt-up construction is that it may be cost-effective – if your building is large enough. Generally speaking, any building or addition less than 50,000 s/f will not be a good fit for tilt-up construction because the economy of scale on materials and equipment doesn’t kick in until one surpasses this threshold (or thereabouts, subject to change based on market conditions). The more materials required, the more the concrete savings may add up.
However, it is easier to achieve one’s code-required insultation R-value in the envelope with an IMP building than a tilt-up concrete structure. Due to these dynamics, it is common for owner-occupants to select an insulated metal panel path while owners who pass utility bills to tenants may be drawn to the short-term savings of concrete. Either way, cost savings are only relevant if one can achieve them without sacrificing primary project goals, which leads us to consider the building’s purpose and design.
Purpose and Design: Tilt-up concrete’s potential construction cost savings often come at a price. For instance, IMP walls may be cut and modified, but modifications to steel-reinforced tilt-up walls are not nearly as easy. Therefore, any desired future changes to the building’s exterior or openings can be problematic with tilt-up.
Also, tilt-up’s cost savings generally rely on meeting insulation requirements without erecting additional interior walls; usually, this strategy only works in situations where the owner isn’t concerned about interior aesthetics (i.e., where exposed insulation is considered an acceptable interior décor). If interior design matters to your organization, the cost savings question may be flipped on its head and the clean finish of IMPs may become the more budget-friendly choice.
Moving from interior to exterior, while there are typically multiple pre-cast exterior patterns available, know that it is harder for your design team to get creative with tilt-up concrete. IMPs can better accommodate features such as exterior glass and variations on panel size, configuration, and texture.
Location and Owner-Specific Concerns: Another key factor to consider is local geography and weather during construction. IMPs are versatile and can be installed in nearly any conditions, but for a tilt-up concrete build, local weather must be amenable to curing the concrete during construction.
Each owner will also have their own unique set of concerns, and as you can see from even this brief overview, the building envelope question of “IMPs or tilt-up concrete” has no single, simple answer. Rather, it involves many angles of consideration, and determining the best envelope for your northeast U.S. warehouse involves careful review of many factors. Consult with an experienced design and construction management firm who will take the time to explore the long-term needs of your site, your building, and your business before deciding on the approach that makes sense for your organization.
Jay Connolly is president of Connolly Brothers Inc., Beverly, Mass.