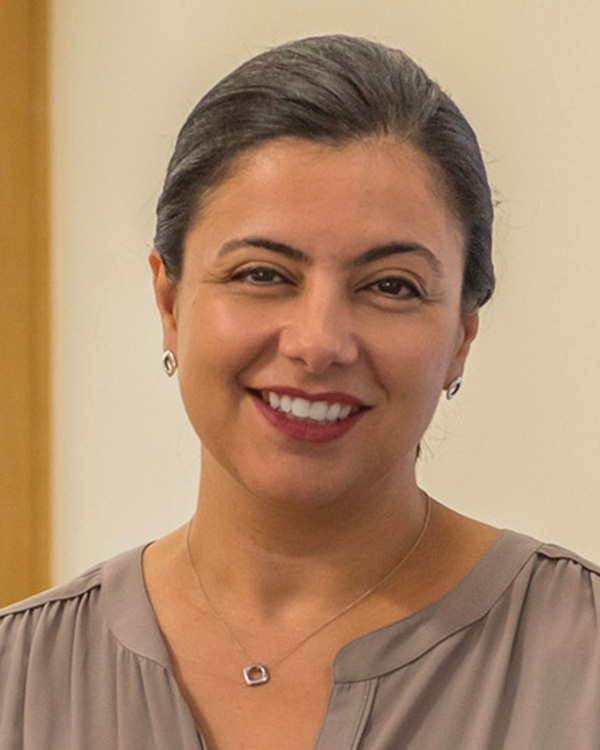
Electrical Services
Virtually everything in our connected world is dependent on the electrical infrastructure, yet we rarely give it a second thought. Except when your phone dies or your lights go off in a storm, and then it is all you can think about. Maybe we should think about electricity that way more often. After all, it powers our economy, keeps us connected across continents, creates mini-climates indoors, the list goes on. Electricity and the infrastructure that carries it are critically important.
In a way, the commercial electrical trade is a victim of its own success at making electricity such an essential part of our everyday world. The electrical industry is busier than ever, and faces challenges as a result: a severe shortage of skilled workers, a record demand for services, increasingly complex projects with tighter and tighter deadlines.
Fortunately, there are some very effective solutions to the big challenges confronting the electrical industry today.
Innovation to the Rescue
Lean manufacturing is a system of continuous evaluation and improvement, of identifying innovative ways of doing things that work best and focusing efforts and resources on those initiatives. Interstate formally adopted lean processes in 2013, but the company has been dedicated to the mission of “continuous improvement” since its founding over 50 years ago.
“Lean means standardizing and building and breaking down your work structure into a smaller packets so that you can manage them more efficiently,” said Mark White, senior design engineer at Interstate.
Lean impacts every group in the company, from Interstate’s design and engineering departments, to the pre-fabrication facility and the jobsite. Electricians can work smarter, safer, and more productively. Customers benefit from quality installations delivered on time and on budget.
“Workflow improvements stem from continuous feedback that Lean promotes,” said Sal Fazio, professional electrical engineer at Interstate.
For all types of projects, communication is critical
With its own engineering and design departments, Interstate does “design-build” projects of all sizes and complexities. Interstate also works with outside engineers and designers on pre-engineered projects, also known as “plans and specs” projects.
As a design-build shop, Interstate oversees all phases of the life-cycle of a project - from conception, to design, to execution. As always, the objective is to install exactly what was designed, on time and on budget. Interstate uses 3D modeling software programs like Revit and 3D CAD to build a detailed model of the project so they can “see” it months before it is built.
“Design-build allows us to know exactly what’s going in up-front. It’s a more efficient process,” said White.
Once design and engineering draw up 3D models of an electrical project, (or if it is a pre-engineered project, has been through coordination), “project detailers” zoom into the drawings and identify what items can be pre-assembled and how the materials and assemblies are to be packaged and delivered. The idea here is to maximize the use of prefabrication across the project and employ “just in time” material delivery strategies as a means of streamlining installation.
Planning for more complexity with less space
On many of today’s jobsites, space is at a premium. Interstate lead coordinator Moe Brunelle has worked for decades as both a field electrician and in the engineering department. He makes sure that all electrical conduits, boards and other assemblies have the “real estate” they need on the jobsite.
“The buildings are becoming tighter and tighter,” said Brunelle. “Everything gets crammed in, and my job is to make sure the electrical components fit, the lighting fits, and all the conduits the switchboards the panel boards have a place to go.”
Means, methods and accountability
The goal of any project is to deliver an installation as designed, on time and on budget. Technology like 3D modeling, pre-fabrication, and onsite laser-guided precision placement helps get the job done faster, better and safer.
The unexpected still happens, and that’s when human judgement and human communication in the field, the operations center, and the design and engineering divisions make all the difference.
“Let’s say for argument’s sake that everything isn’t wonderful and that something in the 3D model is incorrect,” said Fazio. “An electrician in the field can now pull that model up in real-time on a tablet, identify problems, and send the information back to the engineers and the assemblers.”
Fazio reiterates that it’s about three things: means, methods and accountability. “Typically, electricians haven’t had a lot of say in the design process,” said Fazio. “The consulting firm does their thing without worrying about means, methods and accountability, and the electricians in the field do their thing. The difference is that we’re not siloed at Interstate. It’s really a hybrid of communication that takes things to a whole new level.”
Luiza Mills is vice president of human resources for Interstate Electrical Services, Windsor, Conn.