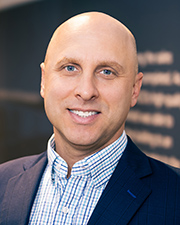
With vacancy rates hitting record lows in the past year and tenants prioritizing speed to market in response to consumer demands, the Boston industrial market has seen dramatic growth, with an increasing number of developments being built on a speculative basis. As the market evolves, many players are changing their warehouse development strategy, especially when it comes to site selection, space utilization and operations, design flexibility, and more.
1. The Boston market is evolving as the construction industry, especially industrial development, continues to see dramatic growth.
Historically, Boston has served as a last mile and consumption market. However, as demand for industrial space continues to grow, it is quickly becoming more of a traditional main distribution market like that of central Pennsylvania or the Carolinas.
Over the past two years, the shift to online shopping sparked by the pandemic has led to major demand for distribution and logistics space as both e-commerce and traditional retailers work to expand their distribution networks nationwide. Further, ongoing supply chain disruptions caused by overwhelmed ports have led to accelerated demand as end-users look to overcome the challenges of just-in-time production networks and mitigate further disruptions by stockpiling input materials and finished goods. This movement toward shorter, more resilient supply chains has further increased competition for prime real estate within the market.
In addition to industrial, Boston is also seeing growth in the life science and biopharmaceutical industries, further increasing competition for site space as developers and owners look to bring new facilities online quickly.
2. With speed to market the highest priority, developers and owners are rethinking their site selection strategy.
Speed to market demands from end-users and supply chain disruptions are causing developers and owners to take a different approach to site selection. As lead times on key materials continue to be long for a variety of resources including steel, roofing, precast concrete, and electrical equipment, contractors like ARCO are working with clients to maximize speed to market by rethinking the sequence in which development activities take place. Previously, a site would be selected, followed by due diligence, entitlement, permitting, and then building. Now, contractors are working with developers and owners to begin ordering materials such as steel and roofing prior to entitlement to mitigate delays and long lead times.
Additionally, many large distribution users are now willing to compromise ideal geographic location for timing benefits. This has led to increased development taking place in markets west of Boston, such as throughout Connecticut, as they offer land availability, as well as access to labor.
Further, Boston, as well as the New England region, has seen a growing amount of speculative development because of immediate demand for space by tenants and end-users.
3. Design flexibility is more important than ever as the need for logistics space with the potential to accommodate changing operations and a variety of end-users increases.
Beyond building square footage, developers and owners are now looking to strategically maximize facility and site flexibility as evolving trends in labor, logistics operations, and automation impact the needs of tenants and end-users.
Factors such as car and trailer parking are becoming increasingly important as warehouse labor has increased more than 150% over the past several years and distributors have fleets larger than ever before. The average number of docks and drive-in doors per facility has also increased to accommodate large distribution operations and automation trends such as conveyor systems that require vehicles to enter the facility.
Additionally, developers and owners are looking to maximize flexibility to accommodate a variety of end-user types, especially GMP as Boston can easily pivot to that market. By choosing to add incremental costs such as upgraded roof structure dead load, floor slab accommodations for future plumbing, and heavier infrastructure into a speculative build, developers can create a facility that is GMP ready.
Further, the speed to market demands of tenants have now led developers to create speculative builds that focus on decreasing time on retrofit. Full dock, lighting, and HVAC packages and speculative office spaces can all be incorporated to ensure tenants are fully operational within the facility as soon as possible.
Unlike traditional delivery methods that treat the phases of design and construction sequentially, the design-build process combines quality of design and construction, management of capital expense, and adherence to schedule all under a single point of responsibility. ARCO’s unique design-build approach removes the risk of overspending on design and construction by providing clients with a firm price proposal. Preliminary design is completed during the proposal process, and owners benefit now more than ever from the speed at which design-build delivery moves.
ARCO is recognized by Engineering News-Record as the #1 domestic builder of distribution and warehouse facilities and the 6th largest design-build general contractor in the United States.
Parker Snyder is the director of business development at ARCO National Construction New England, Framingham, Mass.