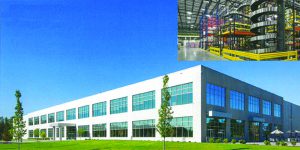
Taunton, MA Wayne J. Griffin Electric has completed work at the new Martignetti Companies facility, a 680,000 s/f wine and spirits distribution center and warehouse with a two-story mezzanine, office space and wine-tasting rooms, located on 115 acres within the Myles Standish Industrial Park.
The new facility has consolidated the distributor’s Braintree and Norwood operations, moving 800 employees to southeastern Mass., with potential future on-site expansion to 1.3 million s/f. Receiving the first retail license for beverage alcohol in Mass. after the repeal of prohibition, this third generation, family–owned business is the leading distributor of wine and spirits in the state and the seventh largest in the country.
The on-site Griffin Electric team, under the direction of senior project manager Wayne Pease, assistant project manager Kelly Sullivan and foreman Dennis Dye and Mike Walsh was responsible for powering the entire facility with two 4000-amp services. Additionally, interior and exterior lighting, a fire alarm system and 600kw gas-powered generator was included in the initial electrical contract for the warehouse. Griffin was also tasked with supplying power to an automated storage and retrieval technology system, which is part of Martignetti’s advanced materials handling operation. The system improves order accuracy and accommodations for growth, and also allows the company to package their product more densely in order to reduce breakage and increase timeliness of deliveries.
Separate contracts secured by Griffin included installations required for a two-story, 140,000 s/f tenant fit-up space and hydrogen plant. The tenant fit-up included lighting and 3000-amp power installations, in addition to systems for fire alarm, ATS, and back-up generator, while the new hydrogen plant with inside dispensing systems included distribution and fire alarms, with Griffin responsible for powering the internal equipment supplied by the project owner.
Serving as the owner’s project manager was C3 – Commercial Construction Consulting Inc. while the general contractor for the warehouse and fit-up projects was Suffolk Construction Co. Inc. working with architect Ware Malcomb and electrical engineer WB Engineering. Nuvera Fuel Cells was in charge of the hydrogen plant project.