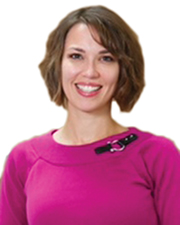
Dowling Houy LLC
It is well known that Boston and Cambridge have become the hub of the biopharmaceutical industry in New England and arguably the world. According to MassBioEd the anticipated job growth rate in Massachusetts research over the next 6 years is 17%. Given the growth of the industry and development of excellent laboratory real estate, many companies are looking to relocate. This can be an overwhelming process for a company of any size and one of the often overlooked keys to the success of these projects is a well maintained laboratory equipment database.
Equipment inventories are often developed in the beginning stages of a project when the lab planning starts. These inventories are used to locate equipment in the new layouts and assure the correct mechanical/electrical and plumbing requirements are accounted for. Companies often hire someone to create this inventory because they don’t currently have one or if they do, it is out of date. However, the time frame from initial planning and actual move in can be 9-18 months. What happens in the meantime can derail a project from running smoothly.
Once the initial database is developed, someone should be appointed to maintain it. This living document will become a useful tool for any lab manager or facilities group not only in lab planning, but equipment maintenance schedules and contacts. Maintaining the list to reflect any changes in equipment and communicating those changes to the team will ensure project success. The fast-paced world of research often means new equipment gets procured while the space is being built out. But who and how is this being communicated to the design / construction team? Just as you have someone tracking the moves/adds/changes to your people database, there should be one point of contact for the equipment database. Showing up at the new site with a full -80 freezer and nowhere to plug it in can be avoided by keeping the inventory up to date and letting the appropriate teams know that it exists and what electrical / alarming requirements it has. The same goes for any equipment that has been replaced as the old gets retired. The cost of having to ‘on-the-fly’ account for these new pieces can greatly impact not just the project budget, but the schedule as well. Discovering you now need to pipe in specialty gases to the lab, weeks after the ceilings were closed, is a conversation worth trying to avoid.
An up to date inventory database provides a great foundation for relocation success. Relocation managers are able to have informed conversations with end users about where their equipment will be located in their new space and confirm the necessary M/E/P requirements are met. Contacting vendors to coordinate equipment preparation and reinstallation is much easier with an accurate database to work from and you do not need to hunt down the information. All parties involved experience time and monetary savings when the information is readily available and not having to be inventoried multiple times to ensure accuracy.
The overall success of a lab relocation has many teams involved. Communication and information are imperative to providing the best outcome. One small tool holds so much power in this process and can be the master key. Never underestimate the power of a good database.
Angela Ciramella is project manager at Dowling Houy LLC, Boston, Mass.