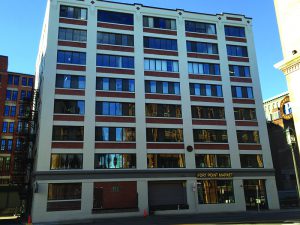
Boston, MA Abbot recently restored the façade of an 8-story mixed-use high-rise building at 389 Congress St. in Boston’s historic Fort Point Channel Landmark district. Built in 1907, the building was originally known as the Boston Wharf Company Building and was used for manufacturing and warehousing. The building is constructed of poured steel reinforced concrete with brick panels under the windows.
Over the years, the rusting of the reinforced steel had caused a significant portion of the concrete to debond away from the building. Recently, the city issued a violation to the owner because of danger to pedestrian and vehicle traffic under the high-rise ordinance. The owner hired an architectural firm (Gorman Richardson Lewis) to evaluate the problem and prepare specifications to repair the façade on all four sides of the building.
In their role on the historical commission, the city was involved in design process to bring the building back to its original aesthetic standards. They researched the historical records and found that the original brick under the windows was painted a natural white color. As part of the city’s mandate, the owner was to repair all concrete based on the architectural specifications and remove the white paint to expose the original red brick color.
A bidding process to determine the masonry contractor ensued, and Abbot was award the contract based on cost, experience, and reputation.
Abbot’s first step was to value engineer the architectural specifications which led to their determination that most efficient approach for materials was to employ a single source manufacturer and recommended the use of Sika Corp. products.
One of the complexities of the repair process was that the demolition of concrete created large cavities and exposed severely deteriorated reinforcing steel. To remedy this issue, it was determined that the new steel had to be anchored into the cavities. Abbot used #3 and #4 corrosion resistant epoxy coated rebar that was epoxy anchored into the cavities to reinforce the new concrete. The material chosen for the repair was a new single-component, self-leveling, pourable polymer- modified concrete mix (Sikacrete 211 SCC Plus).
Following the demolition and installation of steel reinforcing rods, Abbot formed the cavities and installed keyways into the forms to allow a pathway for the new pourable concrete. After the concrete had cured, the forms were removed and very little finishing was needed due to the self-leveling feature of the SikaCrete product. A total of nearly 4,500 s/f of SikaCrete was used in this process covering about 35% of the building.
Logistically, Abbot sequenced the repair by doing one elevation at a time on all four sides of the building. To complicate matters, one side of building abutted an Eversource Energy electrical transformer station. To work around the transformer, Abbot was required to reconfigure a security fence to allow room to stage the area.
Upon completion of concrete repair on the individual elevations, Abbot coated the walls with SikaGard 550W Elastocolor, a high performance elastomeric crack/bridging coating. The Fort Point Channel Landmark District commission chose the color based on a historical photo of building.