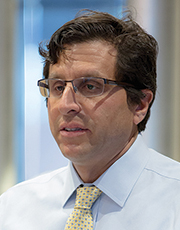
Delphi Construction
As an old school construction manager who has overseen hundreds of millions of dollars of traditional site-built construction, I must admit I was a bit skeptical of modular construction at the start but my recent experience building a $50 million, entirely modular project has made me a believer in the approach and the benefit it can bring to architects, owners and developers.
A $50 million Case Study in Modular Efficiency: Delphi recently completed a large affordable housing project that consisted of the demolition of an existing housing development and the new construction of 49 modular buildings with 200 units spread across 8 separate courts on 42 acres. Our partners were Davis Square Architects and Simplex Modular of Scranton, Penn. The decision to go modular was largely driven by extraordinary time pressures. Traditional construction would have had an overall duration of 36 months. We were able to deliver the finished project in just 21 months.
Real World Benefits Beyond Speed. Clearly one of the greatest benefits of a modular approach is speed. Since manufacturing and site work occur simultaneously projects can be completed in up to half the time as traditional construction. With units being constructed in a climate controlled environment weather delays are also not a factor. But efficient manufacturing means less waste and a smaller carbon footprint as well. And faster does not mean lower quality. Modular buildings are built to meet or exceed the same building codes and standards as site-built structures, and use the same architect-specified materials as conventionally constructed buildings, like wood, concrete and steel.
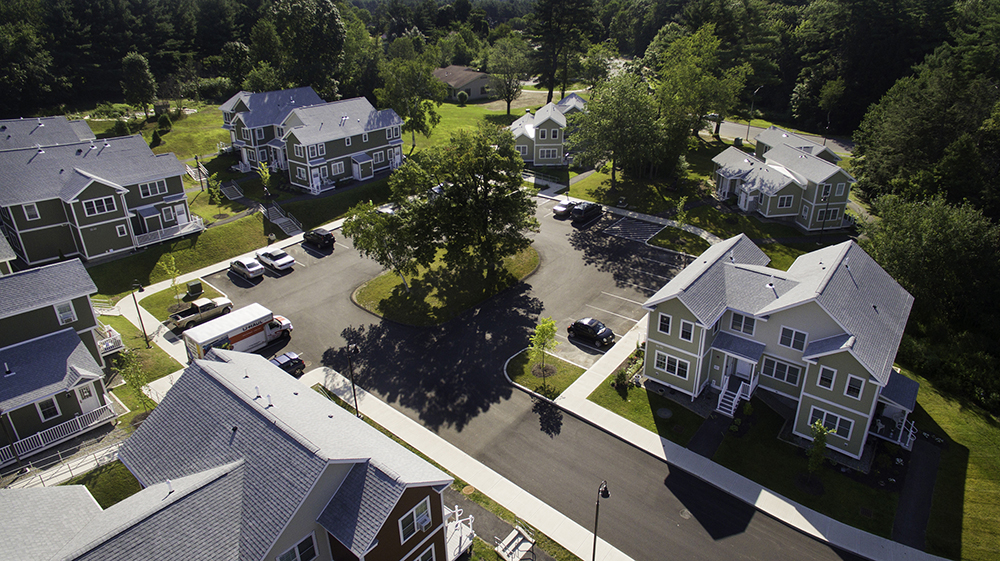
Managing the Schedule is Crucial. Every construction project lives or dies by its schedule. Modular takes that to a whole other level. It’s more akin to supply chain management. You have buildings being designed in one state, permitted and built to order in another, and shipped in by truck exactly when needed. This requires a tremendous amount of coordination between the architect, the manufacturer, our project development team and crews in the field throughout all phases of construction. Above all, it is critical to work out every detail of the plan from the beginning. Many of these activities are being executed months in advance, so the discovery of any needed changes may affect something that already happened months ago.
Debunking the Modular Myths. There are definitely some persistent misperceptions in our industry with regard to modular. I’ve held some of them myself. Modular is of lesser quality, it’s boxy or boring, it’s limited in application, etc. In reality these are based on outdated notions that really do not apply to modern modular construction.
The biggest lesson I learned is that with today’s modular there really does not have to be any trade off in terms of built quality, design flexibility, aesthetics or applications. The speed and cost savings are the result of efficiently managing the supply chain and carefully planning the construction process, not by cutting corners.
Only Do it if You Have a Solid Team. I would encourage owners and architects to consider a modular approach even if it’s not the most obvious solution. A little creativity in the design phase that leverages modular can deliver real benefits to the project.
But only do so if you have the right partners working together from the start. It is absolutely vital that the architect, manufacturer and construction manager work closely together from the earliest phases and throughout the entire project. The success of the project will hinge on the strength and experience of the team.
Joe Mastromatteo is vice president of Delphi Construction, Waltham, Mass.