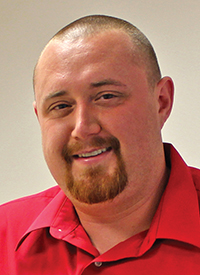
Renovating and upgrading an electrical system can challenge even the best and brightest professional. Given all of the variables in play, unforeseen challenges can emerge at any time and force painful adjustments to project schedules and budget forecasts.
It doesn’t have to be that way. By using lean construction principles and methodologies, combined with prefabrication practices and the latest in three-dimensional design and visualization tools, you can achieve a renovation that has far fewer headaches. Interstate Electrical Services finds that by doing a little planning and sourcing on the front end can keep things running smoothly downstream.
Building trends
Industry-wide, there’s a boom in building renovations. The reasons vary depending on where you look. Companies that are growing and adding more workers usually need more space, which means they should revisit and beef up their electrical systems. Others that want to retrofit an existing building for an entirely new purpose – often called adaptive reuse – almost always need an electrical system upgrade.
Perhaps the most important trend, then, in simplifying your next building renovation is to map the electrical system upgrade to ensure the building takes into account future needs. After all, as the business grows, the building should be ready to accommodate that growth.
Minimizing downtime
At some point during the upgrade, you will probably have to shut the electrical power down. How long you do that, and how well it goes, is worth close study. Without a doubt shutting off the electricity will be felt across the entire enterprise – in production, operations, customer service, safety, security, and so on. The impact can be just like a catastrophic electrical failure.
For this reason, it’s common that most electrical service upgrades are scheduled for a weekend, holiday and other non-business hours.
One way you can minimize downtime is to find a service provider that can design, plan, coordinate, implement, and complete the task all under one roof. This is where the three-part approach comes into play: lean construction principles, prefabrication practices, and 3D, CAD and BIM tools.
Experts suggest you make a systems upgrade plan months in advance of the actual installation date. This will give you an opportunity to move as many tasks upstream in the process and give you a better chance for a smooth, trouble-free installation.
Lean construction
For the past five years, Interstate Electrical Services has been on a journey to learn and apply lean construction concepts and methodologies across its organization. The 50-year old company joined the Lean Construction Institute and adapted lean practices and methodologies into the day-to-day business of its electrical service and construction.
Applying lean principles and methodologies to prepare a building for an electrical systems upgrade can bring many advantages. Lean ensures you work closely with facility managers, building owners, and construction professionals at the planning stage and throughout the entire process.
The lean philosophy also advocates for developing a detailed work plan. The approach used by Interstate is to pre-map the workspace using 3D modeling software to extract and project data points for precise positioning of the electric room spaces and the feeds going in and out. Interstate will also closely study your in-line drawing or create one if yours is outdated or missing.
With lean, you can make sure all parties get an opportunity to review the upgrade process, identify areas of concern and plan for contingencies, from start to finish.
Built, staged, tested, delivered
The final stage in the upgrade is to prefabricate and preassemble the electrical system. When the work can be done off-site, in a controlled setting, the project tends to go much more smoothly. For this reason and others, a few years ago Interstate opened its own operation center.
Under this new model, the electrical system can be built, staged, and functionally tested before it is delivered and installed. If there’s a quality issue, it can be uncovered beforehand, and fixed. In many cases, an entire electrical room can be built, tested, shipped, and delivered to the customer site for installation. Interstate finds this approach saves time, assures quality, reduces downtime, and gets the customer powered up faster than traditional assembly methods for electrical system upgrades.
It’s worth pointing out that both the customer and contractor get value from this bundled approach. With prefabrication, pre-staging, and pre-testing, the customer’s work site has less waste, and is therefore safer since many components, such as light fixtures, transformers, and electrical panels, are assembled off-site.
There are also far fewer lost and damaged parts because most components are transported after they are assembled. Safety is also improved since the typical “hand operations” like conduit bending, wire cutting and splicing take place at an off-site workshop.
Customer benefit
Without a doubt, the biggest benefit of all is the one experienced by the customer. By following this three-part strategy – which includes lean construction principles, three-dimensional design and visualization tools, and prefabrication – you can keep things running smoothly downstream to deliver a much better upgrade.
Just as important, you can avoid the nightmare that everyone fears with an electrical system upgrade. It’s the moment when the project is done, you switch on the power, the system isn’t fully functional, and the troubleshooting and scrambling begin.
Now you know there is a better way.
In Connecticut, Interstate Electrical Services’ team specializes in electrical system upgrades with minimal disruption of the electrical service to your building. Contact the professionals at Interstate Electrical Services today.
Justin Rink is project manager for Interstate Electrical Services, Windsor, Conn.