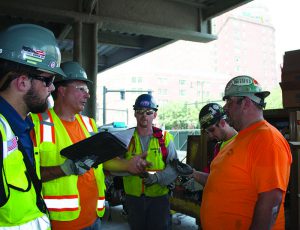
Watertown, MA With a pipeline of roughly $7 billion in projects scheduled to break ground in the near future, yielding approximately 14 million s/f of new development, it’s clear that Boston is riding the wave of a construction boom. With such a wide range of work, from office and residential towers to university expansions, laboratory/research facilities and high-profile projects like the TD Garden expansion and the Wynn Casino, the construction industry is in a unique position to shine under the spotlight. J.C. Cannistraro, one of Boston’s largest mechanical construction firm, has taken a strategic approach to managing this record workload by increasing its capacity for modular prefabrication and doubling down on the principles of safety and lean.
Improving the Construction Industry Until fairly recently, the thought of a better building process appeared to be an unachievable, pie-in-the-sky fantasy. The building process, particularly in the northeast, was very traditional, and despite its inefficiencies, was characterized by “the way things were always done.” The catalyst for industry-wide change occurred with the emergence of building information modeling, which for early-adopters, proved that it was in fact possible to deliver a better quality project. As implausible as it may have seemed, BIM opened the door to new opportunities for companies in the construction trades to improve. In a rigid, plan-and-spec system, companies were using 3D visualization to wring out inefficiencies, reduce mistakes and minimize rework. In the specialty trades, contractors followed the footsteps of larger manufacturers and leveraged BIM for off-site prefabrication as an alternative to “stick building” on site. At Cannistraro, prefabrication began with individual lengths of piping preassembled with all associated pipe valves and fittings. Later, assemblies grew into multi-service piping racks, pre-packaged toilet fixtures, HVAC pump skids on pre-poured concrete inertia bases and now multi-trade Pre-Assembled Modules (PAM) including all plumbing and HVAC piping, ductwork and electrical cable tray. The positive impact of BIM and prefabrication on safety, quality and scheduling caught the attention of more and more people in the industry and soon enough the tide began to turn.
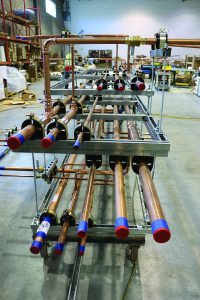
Today, prefabrication is becoming modularized, yet many wonder if the industry is really ready to take the next step. Modular solutions such as pre-assembled fire pump rooms, bathroom pods and pre-packaged mechanical penthouses are the products of lean methods, big-room thinking and collaborative design. Cannistraro has fully embraced these practices on every level and is employing them on its current projects that are currently reshaping both the city and the construction industry. From prefabricated headwall units for an IPD project at Boston Medical Center, to pre-assembled plumbing and duct risers at a new laboratory facility in Kendall Sq., to custom-built Riser Assembly Modules (RAM) at the Seaport Square project in the Innovation District, early collaboration, planning and lean is enabling Cannistraro’s project teams to get creative.
Making Lean Work Although lean practices are nothing new, there is a certain excitement across the construction industry around the idea of managing lean projects, particularly since the widespread adoption of BIM and prefabrication. Becoming lean, however, takes work and requires a change in both thinking and behavior. For lean practices to work, two broad mechanisms must be in place: a team-wide commitment to minimizing waste, and a systematic acceptance and willingness to change. The essence of lean is continuous improvement through the elimination of waste, which often requires that some processes and long-held standards get examined and ultimately changed. Without the buy-in and support from those involved with day-to-day activities, the gears of lean operations will never start to turn. Recognizing these facts, the lean journey for Cannistraro began with training. Comprehensive training in lean principles and practices such as 5S, “5 Why” and Kaizen was provided across all levels of the organization, from the office, to field leadership to the warehouse, shops and its sheet metal partners at Harrington Air Systems.
Armed with this new information, Cannistraro employees were empowered to ferret out waste on their own and identify areas where individual improvement could be applied to their daily work routines, and ultimately make the company better every day. One of the most important elements of lean is recognizing that absolute perfection is never truly achieved, and that there is always room for improvement. It is this mentality, the curiosity/need for continuous improvement, which fuels the engine of a lean operation, and it is becoming more and more prevalent within the walls of Cannistraro and Harrington Air Systems. From the physical layout of the shops, to the inventory system in the tool room, to the naming conventions used for shared project files in the office, no improvement is too small.
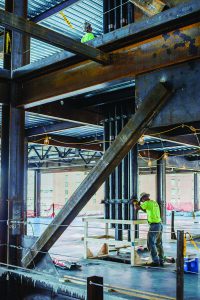
Building with Intelligence ® The upfront commitment and planning involved with Cannistraro’s approach pays off for both the company and its clients in the forms of safer, better quality projects, on-time schedules and an increased trust or peace of mind that the project was delivered the right way. Planning and attention-to-detail are the key components to every aspect of Cannistraro’s work. For example, in coordination, Cannistraro has a VDC Team (Virtual Design & Construction) that acts as the QA/QC for the BIM process which helps modelers, coordinators and designers do their jobs more efficiently and effectively. In the field, foremen stay connected with iPads and iPhones to help them manage both their workload and their teams through tools like the Cannistraro Safety Portal (an app that provides cloud-based access to daily task plans and lesson plans for weekly safety tool box talks). What may seem like even the smallest enhancement often reflects a carefully thought-out process improvement that will enable Cannistraro to keep its people safe and better serve its customers.
The company’s detail-oriented approach to planning and execution is reinforced by its branding statement, “Building with Intelligence®,” a phrase that reflects the firm’s image and reputation. Now in its 53rd year, Cannistraro has become a $205 million company with over 150 office staff, another 500 in the field, and is well-positioned for continued growth in the Greater Boston building industry.